Metallurgical Silicon: The Key to Low-Cost High-Performance Batteries
Currently, almost all lithium-ion batteries utilize graphite materials in their anodes. Graphite was incorporated into lithium-ion batteries in the early 1990s and has been the de facto material ever since. As the key component in the anode, it makes up one of the largest single materials in a battery cell, highly influencing the overall performance and cost of the end product. As a result, battery technologists have been exploring alternatives to graphite, seeking materials that offer better performance at lower costs.
One alternative anode material, silicon, has gained significant attention recently due to its superior specific capacity - 10 times that of graphite - and its abundance and accessibility as the second most prevalent element in the Earth’s crust. In stark contrast, graphite production is dominated by just a handful of countries, with China alone accounting for over 90% of global output. These factors make silicon a highly promising material for next-generation batteries, but inherent issues during charge and discharge cycles have historically prevented its successful integration. Issues however, that have now been overcome through Coreshell's advanced cell technology, enabling the lowest-cost high-performance batteries.
Understanding the Different Grades of Elemental Silicon
Silicon materials exist in various forms and grades, each with distinct properties and applications. In its elemental form, silicon is produced in three main grades: Metallurgical, Solar, and Electronic.
- Metallurgical-grade silicon (MG-Si), with a purity level of 98-99.9% (3N), is the foundational form of elemental silicon. It is primarily used as an alloying agent in the production of aluminum, steel, and copper. MG-Si can also be further purified or chemically processed to produce higher grades of elemental silicon or other forms of silicon, serving as the base precursor for their production.
- Solar-grade silicon (SoG-Si), with a purity of around 99.9999% (6N), is used in solar energy applications, particularly in the manufacturing of solar cells where high purity is essential for optimal performance.
- Electronic-grade silicon (EG-Si), with a purity of 99.9999999% (9N), is the highest purity grade of elemental silicon and is primarily used in the production of semiconductors and integrated circuits. Its extreme purity is crucial for ensuring the performance and reliability of electronic devices, such as computers and smartphones.
Understanding the Different Forms of Silicon
Along with these grades, silicon can be used in specialized forms for specific applications and processes. For instance, in battery anode production, materials such as silicon oxide (SiO) with 99.99% purity and silane gas at 99.9999% purity are predominately used instead of elemental silicon. While still forms of silicon, these variations differ from elemental silicon not only in purity, but also in composition, structure, production methods, and intended manufacturing processes, each tailored to meet specific application needs.
Metallurgical Grade Silicon and How it is Used
Metallurgical-grade silicon (MG-Si) is the most commonly produced type of silicon and serves as the critical foundational component for nearly all silicon grades and forms, from computer chips to silicones and silane gas. It is used in its raw form to enhance metals, purified for critical semiconductor products, and chemically processed to make highly versatile silicone products or support unique manufacturing processes. Coupled with its material abundance, it's truly the most critical form of silicon for almost every application. As a result, there has been growing interest in using metallurgical silicon in its raw form for battery anode production to capitalize on its extremely low material cost and potential to enhance overall battery performance.
How Metallurgical Silicon is Produced
The production of MG-Si begins with quartz or silica sand, both forms of silicon dioxide. Quartz is extremely abundant, making up the second most abundant mineral in the Earth’s crust and is mined all over the world. For MG-Si production, quartz is often preferred over silica sand due to its higher purity and consistency.
The process of making MG-Si is surprisingly simple with very few steps required. Quartz is smelted in a furnace with carbon, which reacts to form silicon and carbon dioxide (SiO₂ + C → Si + CO₂) and once cooled, the silicon solidifies into MG-Si. That’s it. Because quartz is so abundant and the production process is so straightforward, MG-Si is both cheap to produce and widely available.
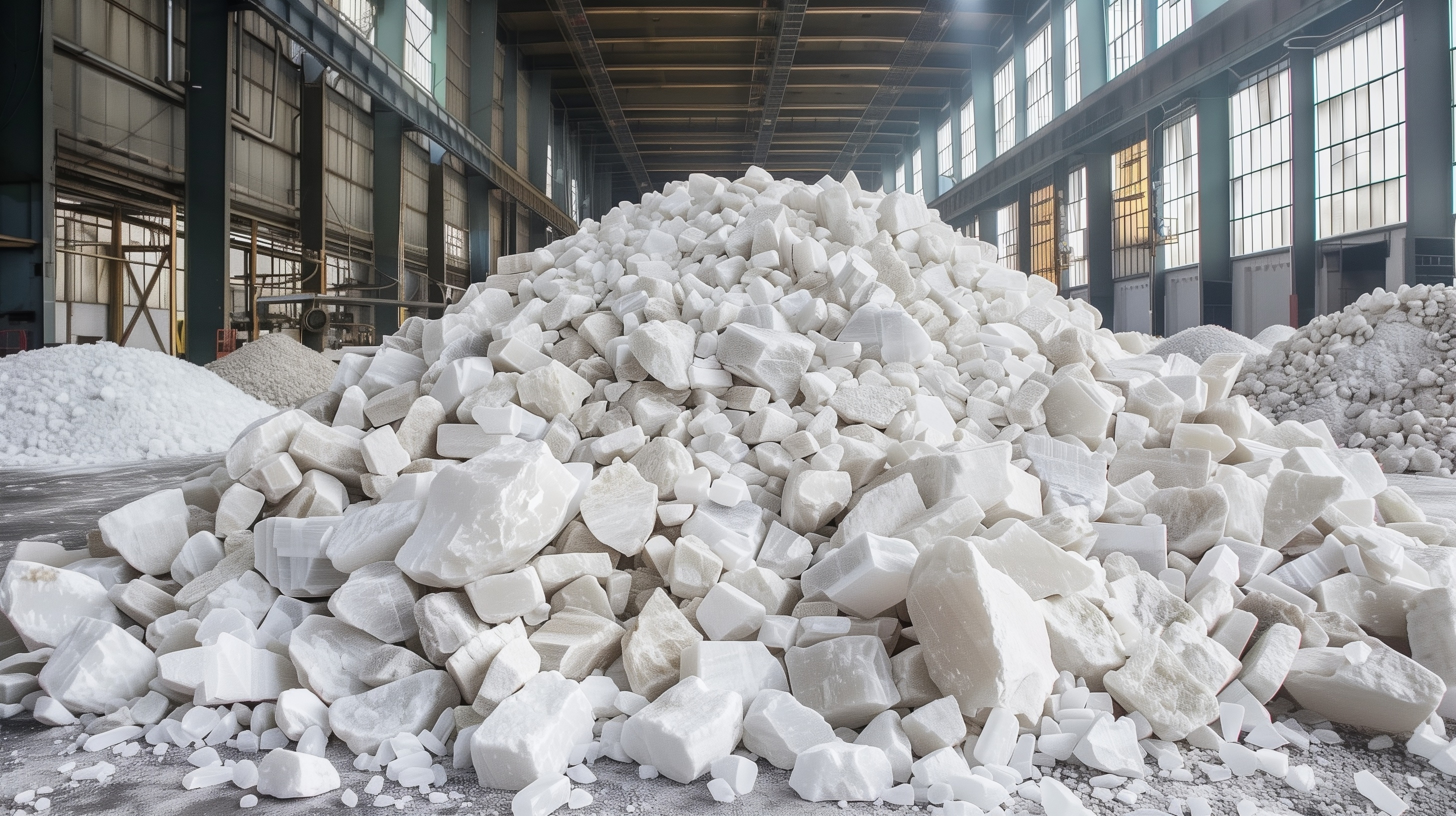
Key Producers of Metallurgical Silicon
While China accounts for over 90% of global output of graphite, MG-Si is produced across the globe in countries including the United States, France, Norway, Brazil, Russia, and China. Notable silicon metal production companies include Ferroglobe, Dow, Elkem ASA, Anyang Huatuo Metallurgy Co, Hoshine Silicon Industry Co, and Mississippi Silicon. This diversity in resource reserve, production locations, and production companies lowers supply chain risks considerably and enables localization of MG-Si production to its downstream products, something that has not been achievable with graphite and other emerging battery materials.
How MG-Si Differs from Other Silicon Technologies in Battery Production
Other battery-grade silicons, such as SiO and silane, require more complex production methods. SiO, which is produced via an additional step of co-evaporation of MG-Si with SiO₂, is more stable in battery applications but needs additional pre-lithiation to improve poor first-cycle efficiency. Silane on the other hand, is derived from MG-Si through successive chlorination and high-temperature reduction processes, yielding silane gas. This gas is then typically used in a chemical vapor deposition (CVD) process utilizing specialized production equipment to create silicon thin-film coatings and/or nano-deposits, an extremely energy-intensive process. In the case of battery materials, the silicon is typically deposited onto carbon matrices, the end product sometimes called Composite Silicon. While these methods offer some advantages, they make SiO and silane-derived silicon significantly more expensive than MG-Si and only offer a replacement for a minority portion of graphite in the battery anode.
The Potential Benefits and Current Challenges with MG-Si in Batteries
MG-Si offers higher specific capacity than graphite - and at a lower cost than both graphite and other silicon technologies. Along with this, it is already produced in hundreds of thousands of tons annually and can be easily scaled to even larger volumes due to its material accessibility and ease of manufacturing, making it capable of supporting widespread adoption. This is in contrast to other emerging battery and silicon technologies that do not have the material production capacity or infrastructure to support production at scale, and will require major investments and time to be able to stand up. While these benefits have made MG-Si a focus for use in battery anodes, it has faced challenges that have prevented its successful integration and adoption.
The major issue with silicon is the volume expansion and contraction that occurs during lithium-ion cycling which causes stress, cracking, and degradation. Additionally, an unstable solid electrolyte interphase (SEI) can cause capacity loss over time. These issues have proven difficult to overcome with MG-Si, and so to combat them, a more stable form of silicon is used, like SiO, or silicon is deposited as nano-sized particles from silane gas, which are less likely to fracture. This provides the increased energy capacity of silicon, but effectively loses its supply chain and cost benefits.
Finally - A Breakthrough with MG-Si
To fully capitalize on the cost, supply chain, and capacity benefits of silicon, Coreshell aimed to enable the use of silicon in its raw metallurgical grade form. Through breakthrough innovation validated by early production, Coreshell has developed a state-of-the-art solution-phase deposition process - applied with standard battery production equipment - that successfully overcomes the challenges previously associated with MG-Si in batteries. A key aspect of this innovation is the use of mechanically-milled, micron-sized and non-uniform silicon particles—an important advancement that significantly lowers costs and enhances scalability. This allows for the direct use of 100% MG-Si in the anode, with no need for costly refining steps. Coreshell’s technology also extends beyond the anode, incorporating unique advancements in the electrolyte, binders, and other key components, all tailored specifically to enable the use of 100% MG-Si without additional significant costs or unique manufacturing processes and equipment.
As a result, Coreshell has achieved a major breakthrough with the industry’s first commercial-scale 60 Ah battery cells using 100% domestically-sourced metallurgical silicon. By revolutionizing the entire cell design, Coreshell harnesses the power of silicon anodes and low processed metallurgical silicon, adding 30% more capacity while decreasing cost by up to 25%. This breakthrough enables the production of the lowest-cost high-performance batteries, offering a transformative solution that could dramatically reduce the price of electrification. By utilizing domestically sourced metallurgical silicon, Coreshell addresses cost, supply chain, and performance challenges simultaneously. These advancements make it possible to scale production at a competitive price point, ultimately driving down costs for consumers, increasing energy density, and extending battery life. With these enhancements, mass electrification becomes not just possible, but increasingly inevitable.